“Robotics” is a confluence science using the continuing advancements of Mechanical Engineering, Material Science, Sensor Fabrication, Manufacturing Techniques and Advanced Algorithms. The study and practice of robotics will expose professionals to hundreds of different avenues in the areas of Innovation and Automation. Robotics brings forth a magical curiosity of the world leading to creation of amazing machines.
Definition: Robotics can be defined as the science or study of the technology primarily associated with the design, fabrication, theory, and application of robots, other areas which contribute includes knowledge of mathematics, techniques and components enable robotics to create the magical end product. The practical applications of robots drive development of robotics and drive advancements in other sciences. The promise of robotics is easy to describe but hard for the mind to grasp.
Robots hold the promise of moving and transforming materials with the same momentum and ease as a computer program transforms data. Today, robots mine minerals, assemble semi-processed materials into automobile components, and assemble those components into automobiles. On the immediate horizon are self-driving cars, robotics to handle household chores, and assemble specialized machines on demand. It is not unreasonable to imagine robots that are given some task, such as reclaim desert into photo voltaic cells and arable land, and left to make their own way. Then the promise of robotics exceeds the minds grasp. In summary, robotics is the field related to science and technology primarily related to robotics. It stands tall by standing the accomplishments of many other fields of study.
About Robotics
Robotics spans multiple scientific and engineering disciplines, when an enthusiast want to design a better robot, he/she should get some basic knowledge. How much one should learn depends on how complex one wants to make a robot.
Example: A small tethered tabletop robot would only require some basic knowledge in electronics and programming,a shoe box sized robot would require some additional knowledge on mechanics (mostly about balance) and a large robot might even require some knowledge on solid mechanics. This page covers the fields that are very much used in robotics. You don’t need to know everything about all of these subjects, however knowing the basics of each of these fields can help in building better robots and prevent you from making (some of the) beginner’s mistakes.
Robotics - Getting Started
What an Enthusiast should know
Mechanics - 
Mechanics helps keeping a robot in balance. Although one could build a robot without knowing anything about mechanics, it’ll help in preventing your robot from tipping over when turning, or when picking up something. Another point where mechanics pays off are axles. On small robots you can attach the wheels directly to the output shaft of the motor. However this doesn’t work well for larger robots as this puts a lot of stress on the internals of the motor. A better way is to attach the wheel to an axle, and use gears to connect the motor to the axle. Knowledge of mechanics allows you to build such constructs. If robot is a small line follower almost any building material will work. However if your robot weighs a few kilos, something sturdier than cardboard and soda sippers is appropriate. And if a robot is human size one should consider metal and/or composite construction.
Knowledge of Mechanics helps you understand key areas within Robotics stream which is about:
- How forces are transferred between the different parts of a construction.
- Where the center of gravity lies.
- Friction
- Position, speed, acceleration
- Inertia
- Material properties
Solid Mechanics
Solid mechanics is about how forces distribute inside solid materials. Knowledge about this subject is useful because it explains how materials respond to loads. This helps to prevent using too thick or too thin materials. This isn’t required for small or medium robots, but it allows to be more efficient with building materials and gives insight to why and how materials fail (break and/or deform). for a start on solid mechanics.
Electronics
Electronics is critical, you can’t go without (unless you want to build a complete mechanical robot or use pneumatic for control). Today there are plenty of books covering basic electronics
Understanding of Electronics is mainly in the areas of:
- Electronic Components
- Analog Circuits
- Digital Logic
- Micro Controllers
Programming
Computer programming essential in micro controllers. Although it might sound difficult, it can be very easy in practice (for most purposes). Understanding of programming is mainly on the areas of:
- Control structures (sequence, selection, iteration)
- Data types (constants, variables, integers, real, string,...)
- Algorithms
- Hardware control (setting and reading registers, interrupts,...)
- Logic
Much of this comes down to setting bits in a byte using simple Boolean logic, and writing this value into some register or memory location. Higher level languages like Bascom provide hardware addressing as special variables, which can be treated just like any other variable.
Microcontrollers (and processor boards) are one of the areas where using Assembly is still very valid. Memory (both RAM and program space) is very limited in these, although each new generation of microcontroller has more memory for about the same price. Many microcontrollers provide speed between 2K and 30K, and processor boards tend to have up to 256K. These numbers vary wildly, but are still significantly less than PCs have. However if you don’t know an assembly language, most microcontroller and processor boards have high level language compilers available in many flavors.
Robot programming is also about:
- The Event Loop: Most microcontrollers do not have the resources for threading. One will need to look at a robot’s task within a fraction of a second at a time, and choose which small action to take. What can the program do in that moment to get a little bit closer to its goal?
- Interpreting sensor data: Sensors have many ways of providing noisy or misleading information; how many types of errors are acceptable? Dirt in a rheostat, a broken switch, and a venetian blind flickering on a photodiode are obvious faults. How about temperature drift, non-linear response curves, or your robot seeing its own shadow?
- Decision making or Artificial Intelligence is the art of making the right decision given the constraints of the current system.
- Motors and motion: Making motion on a robot often involves moving several motors at once, often with feedback from sensors
Artificial Intelligence
AI is the most sought after area in the Information Technology space. But still has a very long way to go, AI isn’t just about getting a computer to think and reason. It’s more about ordering, sorting and organizing knowledge in a machine and constructing algorithms for extracting real world conclusions from these databases. A search engine like Google Deepmind or IBM Watson are some of the best examples in the industry of AI.
Artificial Intelligence (in Robotics) is about:
- Finding the shortest way between 2,3 (or more) points
- Dealing with obstacles
- Handling new situations (machine learning)
Mathematics
Although math is generally seen as the ultimate theoretical science, it can be one of the most important skills in many of the more advanced domains of robotics. e.g. Mechanics uses a lot of math. For simple constructs you won’t need much more than high school level math, for more complicated shapes it becomes necessary to use more complex math tools like integrals. But since robotics is a very practical craft many things can be done with approximations. Math however can be very helpful in making the right approximation.
Critical Components for building a Robot
Power source
At present, mostly (lead–acid) batteries are used as a power source. Many different types of batteries can be used as a power source for robots. They range from lead–acid batteries, which are safe and have relatively long shelf lives but are rather heavy compared to silver–cadmium batteries that are much smaller in volume and are currently much more expensive. Designing a battery-powered robot needs to take into account factors such as safety, cycle lifetime and weight. Generators, often some type of internal combustion engine, can also be used. However, such designs are often mechanically complex and need a fuel, require heat dissipation and are relatively heavy. A tether connecting the robot to a power supply would remove the power supply from the robot entirely. This has the advantage of saving weight and space by moving all power generation and storage components elsewhere. However, this design does come with the drawback of constantly having a cable connected to the robot, which can be difficult to manage. Potential power sources could be:
- pneumatic (compressed gases)
- Solar power (using the sun's energy and converting it into electrical power)
- hydraulics (liquids)
- flywheel energy storage
- organic garbage (through anaerobic digestion)
- nuclear
Actuation
- Electric motors
- Linear Actuators
- Series elastic actuators
- Air Muscles
- Muscle Wire
- Electroactive Polymers
- Piezo motors
- Elastic Nanotubes
Sensors
Sensors allow robots to receive information about a certain measurement of the environment, or internal components. This is essential for robots to perform their tasks, and act upon any changes in the environment to calculate the appropriate response. They are used for various forms of measurements, to give the robots warnings about safety or malfunctions, and to provide real-time information of the task it is performing.
Touch
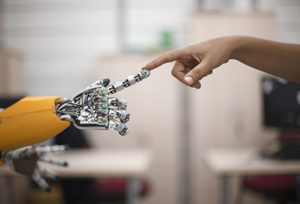
Current robotic and prosthetic hands receive far less tactile information than the human hand. Recent research has developed a tactile sensor array that mimics the mechanical properties and touch receptors of human fingertips. The sensor array is constructed as a rigid core surrounded by conductive fluid contained by an elastomeric skin. Electrodes are mounted on the surface of the rigid core and are connected to an impedance-measuring device within the core. When the artificial skin touches an object the fluid path around the electrodes is deformed, producing impedance changes that map the forces received from the object. The researchers expect that an important function of such artificial fingertips will be adjusting robotic grip on held objects.
Scientists from several European countries and Israel developed a prosthetic hand in 2009, called SmartHand, which functions like a real one—allowing patients to write with it, type on a keyboard, play piano and perform other fine movements. The prosthesis has sensors which enable the patient to sense real feeling in its fingertips.
Computer Vision
Computer vision is the science and technology of machines that see. As a scientific discipline, computer vision is concerned with the theory behind artificial systems that extract information from images. The image data can take many forms, such as video sequences and views from cameras.
In most practical computer vision applications, the computers are pre-programmed to solve a particular task, but methods based on learning are now becoming increasingly common.
Computer vision systems rely on image sensors which detect electromagnetic radiation which is typically in the form of either visible light or infra-red light. The sensors are designed using solid-state physics. The process by which light propagates and reflects off surfaces is explained using optics. Sophisticated image sensors even require quantum mechanics to provide a complete understanding of the image formation process. Robots can also be equipped with multiple vision sensors to be better able to compute the sense of depth in the environment. Like human eyes, robots' "eyes" must also be able to focus on a particular area of interest, and also adjust to variations in light intensities.
There is a subfield within computer vision where artificial systems are designed to mimic the processing and behavior of biological system, at different levels of complexity. Also, some of the learning-based methods developed within computer vision have their background in biology.
Manipulation
- Mechanical Grippers
- Vacuum Grippers
- General purpose Effectors
Locomotion
Locomotion is about movement or the ability of movement from one place to another.
- Rolling Robots
- Two-wheeled Balancing Robots
- One-wheeled Balancing Robots
- Spherical Orb Robots
- Six-wheeled Robots
- Tracked robots
Walking applied to Robots
Walking is a difficult and dynamic problem to solve. Several robots have been made which can walk reliably on two legs, however, none have yet been made which are as robust as a human. There has been much study on human inspired walking, such as AMBER lab which was established in 2008 by the Mechanical Engineering Department at Texas A&M University. Many other robots have been built that walk on more than two legs, due to these robots being significantly easier to construct. Walking robots can be used for uneven terrains, which would provide better mobility and energy efficiency than other locomotion methods. Hybrids too have been proposed in movies such as I, Robot, where they walk on two legs and switch to four (arms+legs) when going to a sprint. Typically, robots on two legs can walk well on flat floors and can occasionally walk up stairs. None can walk over rocky, uneven terrain. Some of the methods which have been tried are:
- Zero Mount Point Technique
- Hopping
- Dynamic Balancing (controlled falling)
- Passive Dynamics
Other methods of Locomotion
- Flying
- Snaking
- Skating
-
Climbing
- Swimming (Piscine)
- Sailing
Human-robot Interaction
This is basically about how machines interact with humans viz.systems, services, environments. Typically, human interaction with machines is at various several touch points, enabling machines to understand this interactions is the key for the correct outcomes. In Robotics, human interaction is all about:
- Speech Recognition
- Robotic Voice
- Gestures
- Facial Expression
- Artificial Emotions
- Personality
- Social Intelligence
Robotics: Global Market Synopsis and Future Trends - 2018 to 2025:
The global market for robotics is expected to display double-digit growth in the upcoming years, thanks to the increasing automation across industries. Automation is increasingly becoming the buzzword across labor-intensive industries that are grappling with rising labor costs and lack of skilled workforce issues. This has pushed the adoption of robotic technology to automate operations. Industrial robots, for instance, are deployed in manufacturing and production settings to perform an array of programmed tasks.
As per a report by Transparency Market Research (TMR), the revenue for global robotics market will be worth US$147.26 billion dollars by 2025 end and rising at a healthy 17.4% CAGR over the period from 2017 to 2025. the market is expected to reach an amount of 2,731.2 thousand units by 2025.
Static Robotics
The key segments of the worldwide robotics market depending upon type are mobile robotics, exoskeleton, and static robotics. Of them, in 2016, the segment of static robotics led the market in terms of both value and volume. Going ahead, the static robotics segment is anticipated to register the leading growth rate over the forecast period between 2017 and 2025.
The primary applications of robotic products include
- Logistics
- Personal
- Military
- Last mile mobility
- Agriculture
- Construction / Mining
- Entertainment
- Medical
- Research
The leading component segments of the global robotics market considered in this study are into:
- Sensors
- Control units
- Actuators
- Brake systems
- Vision systems
With the increasing demand for enhanced sensing capabilities of robots, sensors are anticipated to display significant growth over the forecast period.
Global Market Growth - (Growth Rate through 2025)
The robotics market is classified on the basis of geography into North America, Asia Pacific, Europe, Latin America, and the Middle East and Africa.
Asia Pacificheld the leading share in the robotics market in 2017 and is anticipated to rise at a significant rate over the forecast period of 2018 to 2025. This is mainly because of incessant innovation and development in the field of robotics leading to its widespread application across industries. The Asia Pacific robotics market is also anticipated to gain from the advent of nano-technology in robotics in the future. Moreover, the introduction of collaborative robots that have substantially upped productivity in manufacturing, material handling, medical, and automotive sectors with less human labor will benefit the growth of this regional market over the forthcoming years.
North America is estimated to display a relatively higher-paced growth in the upcoming years. The region being home to a large number of robot manufacturers, along with contracts from government agencies and defense forces, is leading to consistent innovation and development in robotics technologies, which is aiding the growth of North America robotics market. Further, the increasing uptake of service robots among consumers to reduce workload is also expected to benefit the North America robotics market in the next few years.
Top 20 - Global Market Players in the global robotics market -
- Fanuc Corporation,
- Clearpath Robotics Inc.,
- Barrett Technology LLC,
- John Deere,
- Kuka AG,
- Honda Motor Co. Ltd.,
- Boeing,
- Bossa Nova Robotics,
- Seegrid Corporation,
- Aetheon Inc.,
- Google Inc.,
- Swisslog,
- Northrop Grumman Corporation,
- iRobot Corporation,
- Lowe’s,
- Omron Adept Technologies,
- Amazon,
- Fetch Robotics Inc.,
- Savioke,
- Locus Robotics.
[1] Electronics - https://en.wikibooks.org/wiki/Theoretical%20Mechanics 2 https://en.wikibooks.org/wiki/Electronics [2] Solid Mechanics - http://en.wikibooks.org/wiki/Solid_ Mechanics [3] Robotics Components - https://en.wikipedia.org/wiki/Robotics [4] Global Robotics Industry Outlook - https://www.transparencymarketresearch.com/robotics-market.html [5] Edx - Robotics - https://www.edx.org/learn/robotics
Leave a Reply