3D printing is also referred to as additive manufacturing, is a process of making three dimensional objects from a computer based design. The creation of a 3D printed object is achieved using additive processes.
3D printing is the opposite of subtractive manufacturing which is cutting out / hollowing out a piece of metal or plastic with for instance a milling machine. 3D printing enables you to produce complex shapes using less material than traditional manufacturing methods. In an additive process an object is created by laying down successive layers of material until the object is created.
The term “3D printing” covers a variety of processes in which material is joined or solidified under computer control to create a three-dimensional object, with material being added together (such as liquid molecules or powder grains being fused together), typically layer by layer. One of the key advantages of 3D printing is the ability to produce very complex shapes or geometries, and a prerequisite for producing any 3D printed part is a digital 3D model or a CAD file.
How does 3D Printing Work?
Computer Based Design or Modeling
3D printable models may be created with a computer-aided design (CAD) package, via a 3D scanner, or by a plain digital camera and photogrammetry software. 3D printed models created with CAD result in reduced errors and can be corrected before printing, allowing verification in the design of the object before it is printed. The manual modeling process of preparing geometric data for 3D computer graphics is similar to plastic arts such as sculpting. 3D scanning is a process of collecting digital data on the shape and appearance of a real object, creating a digital model based on it.
Slicing: From 3D Model to 3D Printer
Slicing is dividing a 3D model into hundreds or thousands of horizontal layers and is done with slicing software. Some 3D printers have a built-in slicer and let you feed the raw .STL, .OBJ or a CAD file.
When your file is sliced, it’s ready to be fed to your 3D printer. This can be done via USB, SD or internet. Your sliced 3D model is now ready to be 3D printed layer by layer.
3D printing technologies 
There are several different 3D printing technologies. The main differences are how layers are built to create parts. SLS (selective laser sintering), FDM (fused deposition modeling) & SLA (stereolithograhpy) are the most widely used technologies for 3D printing. Selective laser sintering (SLS) and fused deposition modeling (FDM) use melted or softened materials to produce layers.
3D printer
A 3D printer is unlike your standard, 2D inkjet printer. On a 3D printer the object is printed in three dimensions. A 3D model is built up layer by layer. Therefore the whole process is called rapid prototyping, or 3D printing. The resolution of the current printers is around 328 x 328 x 606 DPI (xyz) at 656 x 656 x 800 DPI (xyz) in ultra-HD resolution. The accuracy is 0.025 mm - 0.05 mm per inch. The model size is up to 737 mm x 1257 mm x 1504 mm.
The biggest drawback for the individual home user is still the high cost of 3D printer. Another drawback is that it takes hours or even days to print a 3D model (depending on the complexity and resolution of the model). Besides above, the professional 3D software and 3D model design is also in a high cost range). Alternatively there are already simplified 3D printers for hobbyist which are much cheaper. And the materials it uses is also less expensive. These 3D printers for home use are not as accurate as commercial 3D printer.
Difference between a basic rapid prototyping machine and a 3D printer
3D printers are the simple version of rapid prototyping machines. It is lower lost and less capable. Rapid prototyping is a conventional method that has been used by automotive and aircraft industries for years.
In general 3D printers are compact and smaller than RP machines. They are ideal for use in offices. They use less energy and take less space. They are designed for low volume reproduction of real objects made of nylon or other plastics. That also means 3D printers make smaller parts. Rapid prototyping machines have build chambers at least 10 inches on a side, a 3D printer has less than 8 inches on a side. However a 3D printer is capable of all the functions of rapid prototyping machine such as verifying and validating design, creating prototype, remote sharing of information etc.
Consequently 3D printers are easy to handle and cheap to maintain. You can buy one of those DIY kit in the market and build up yourself. It is cheaper than the professional rapid prototyping, for $1000 or less you can have one 3D printer. While the professional rapid prototyping cost at least $50,000.
3D printers are less accurate than rapid prototyping machines. Because of its simplicity the material choices are also limited.
Future of 3D Printing
3-D printing is an high potential industry. Not too long ago, the printing speed and limited output of 3-D printers made them suitable only for rapid prototyping. In the coming years, 3-D printers will be at the heart of full-scale production capabilities in several industries, from aerospace to automotive to health care to fashion. Manufacturing as we know it will never be the same.
Decades of innovation have led to the 3-D printing revolution. Recent advancements in speed, printing technology and material capabilities are now aligned, and together they will push the entire industry forward. Along with growing competition and investment in the 3-D printing industry, these new capabilities will reshape custom manufacturing. The 3-D printing industry is on the verge of another tipping point, and here are the reasons why.
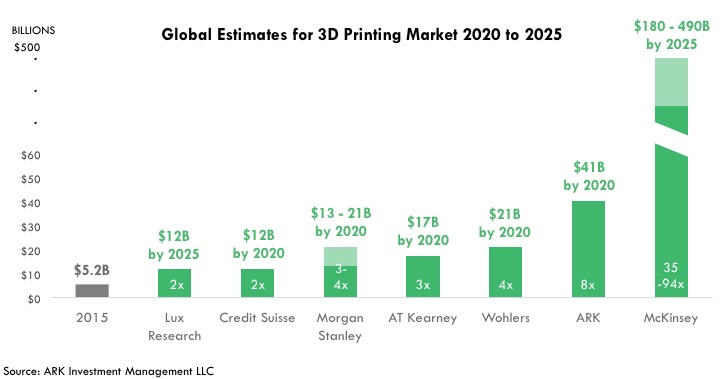
Direct-metal printing is getting faster and more capable, and many new technologies are now coming into play. The number of metal alloys that can be 3-D printed is on the rise, and they have exceptional performance characteristics. You can get high-performance light-weighting and complexity that is impossible with traditional design and manufacturing processes. With these changes, imagine the possibilities: Complex and highly detailed products critical for the aerospace, automotive and mechatronic industries will soon be available for production at a fraction of the cost. If your car needs a repair, you’ll soon be able to purchase a shift knob or fuel-door hinge pin that was quickly and inexpensively printed. Aerospace engineers will use the same technology to produce jigs and fixtures for spacecrafts. The implications are staggering. What’s more, there are fully automated, multi-station direct-metal printers that are essentially an entire factory in a box. With automated parts changes and material replenishment, they can literally operate around the clock.
GE is a major player in the direct-metal printing field, and the company predicts that its metal business alone will surpass $1 billion in annual revenue in the next couple years. And early-stage companies such as Desktop Metal and Markforged have received several hundred million dollarsin funding to deliver entry-level direct-metal systems that print from a metal-plastic filament.
For decades, 3D printing has been capable in terms of geometric precision and accuracy, but printing speeds remained very slow. But this too is changing. The CLIP technology from Carbon 3D and similar technologies from companies like one of mine, Nexa 3D, are capable of continuously printing photo-curable polymers at very high speeds -- 40 or 50 times the speed of a conventional stereolithography 3-D printing system.
With the ability to print a centimeter every minute, these systems will no doubt play a major role in the design-to-manufacturing cycle. While a similar job used to take days, now you can get parts in your hand in five, 10 or 15 minutes. It will also unleash work with completely new chemistries, particularly within several variants of urethane. You can make the output rigid, semi-rigid or flexible, and these kinds of variations in chemistry open up a lot of end-use applications, from athletic shoes to vehicle interiors to apparel.
Innovations In Selective Laser Sintering
Selective laser sintering (SLS) is the ability to produce parts from a variety of nylon materials. It’s been practiced in a few industries for decades now. Take the F-18 fighter jet: Every F-18 in service today has been flying with SLS parts for air ducts, electronics covers and many other components for a couple of decades. So that’s not headline news.
But as of late, companies such as HP have entered the market with technology that speeds up production of selective laser-sintered parts. Again, we’re talking dozens of times faster than traditional SLS machines. It will help bring selective laser sintering into the mainstream instead of just confining it to hyper-specific applications like the F-18.
With the advent of these faster machines, companies can increase manufacturing speed and manufacturing scale with significantly more affordability. It’s no longer reserved for exotic military, defense and aerospace applications. It’s ready to go mainstream.
How These Innovations Will Shape The Future
When you combine all these advancements with infinite computing power in the cloud, IoT connectivity, big data and next-generation robotics, you arrive at the realization of Industry 4.0: a truly cognitive, adaptive and largely self-optimizing factory. And this huge development will largely be catalyzed and fueled by additive manufacturing.
In some industries, 3-D printing has been considered or utilized for several decades. However, the use cases have primarily been in design and prototyping. Industries that have a great deal of familiarity with this technology such as aerospace and automotive are beginning to unlock these capabilities so that others can create working tools, fixtures, jigs and end-use parts. They are just beginning to scratch the surface of 3-D printing for outright manufacturing.
Many companies will also invest in continuous photopolymer systems. Gartner expects the growth in photopolymer 3-D printers over the next couple years to be in the neighborhood of 75%.In sectors such as health care and personalized medical devices, more and more 3-D printers are being used to create hearing aids, dental fixtures, hip replacements, medical implants and surgical tools.High-speed photopolymer systems are ideal for dental applications, while direct-metal and SLS solutions are a better fit for certain implants.
Perhaps most importantly, another trend that is taking shape is that 3-D printers are now becoming mainstream presences in schools and public libraries. Children aren’t just learning how to use 3-D printing hardware and design software; they’re expecting to be able to use it.
An industry once considered a gimmick is proving itself to be a formidable giant. Make no mistake: 3-D printing will be a force that upends nearly every industry over the coming decade, and its influence is exciting and unstoppable.
Leave a Reply